Table of Contents
Introduction
3D printing, often referred to as additive manufacturing, has paved the way for crafting objects from diverse materials rooted in digital blueprints. Transforming manufacturing and design realms, it’s empowered both entities and individuals to materialize their innovations. Initially synonymous with plastic, the advent of metal 3D printing has broadened the spectrum of opportunities.
Understanding 3D Printing
Originally a tool for prototyping, 3D printing metamorphosed into a versatile avenue for generating a multitude of items. The essence of the technique is sequential creation, building objects layer upon layer. This is orchestrated by specialized devices that materialize objects based on 3D schematics.
Significance of Metal 3D Printing
Metal 3D printing signifies the evolution of this domain. While traditional plastic-based 3D printing poses certain constraints concerning resilience and application in critical scenarios, the metal variant transcends these barriers. This not only facilitates the manufacturing of intricate metallic shapes, often challenging or unattainable via orthodox metalwork methods but also heralds newfound avenues in diverse sectors like aerospace, automotive, and health.
Tracing its Roots
Exploring metal 3D printing’s journey unveils a notable metamorphosis, transitioning from rudimentary research endeavors to becoming a cornerstone of global industrial innovation.
From Conception to Modern-day Relevance
The 1980s witnessed the dawn of 3D printing, with stereolithography spearheading the movement. This method employed ultraviolet lasers to convert digital designs into tangible plastic entities.
Metal printing’s inaugural successes emerged in the subsequent decade. Breakthroughs like Direct Metal Laser Sintering (DMLS) paved the way for crafting intricate metal components straight from metallic powders. These were synthesized using lasers that meticulously sintered or melded metal powder, layer by layer.
With the passage of time, both the quality and pace of the printing process witnessed significant enhancements. By the early 21st century, technological advancements coupled with a reduction in equipment expenses made metal 3D printing a feasible option for industry giants.
In the contemporary industrial landscape, metal 3D printing stands as a vital component. A myriad of sectors, encompassing aerospace, automotive, healthcare, and the realm of jewellery, have harnessed its potential, with the technology promising innovation, economic efficiency, and elevating production paradigms.
Key Metal 3D Printing Technologies
Metal 3D printing encompasses a variety of pivotal technologies, each boasting distinct features, applications, merits, and demerits. Here’s an overview of the primary ones:
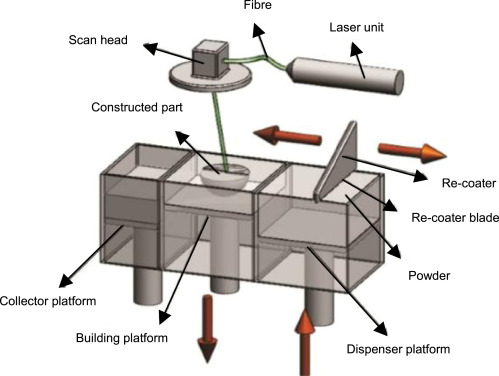
Direct Metal Laser Sintering (DMLS)
Principle: Utilizes a laser to melt metal powder, layer by layer. Upon melting one layer, the subsequent layer is added.
Advantages: Exceptional accuracy, capability to produce intricate parts, and minimal waste.
Disadvantages: High-cost procedure and necessitates post-printing processing.
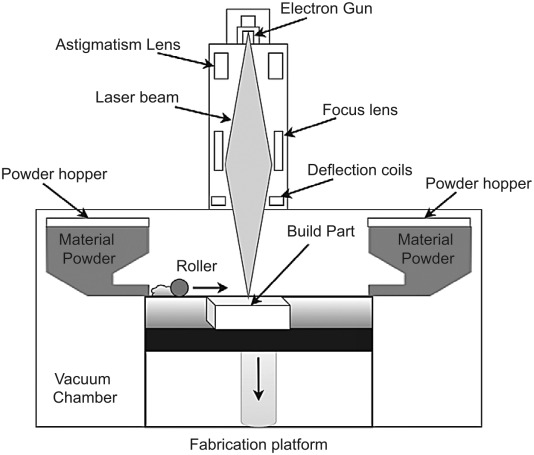
Electron Beam Melting (EBM)
Principle: An electron beam fuses metal powder within a vacuum chamber.
Advantages: Compatible with dense and high-melting-point metals, induces lesser stress in the resultant material.
Disadvantages: The procedure is time-consuming and the equipment is costly.
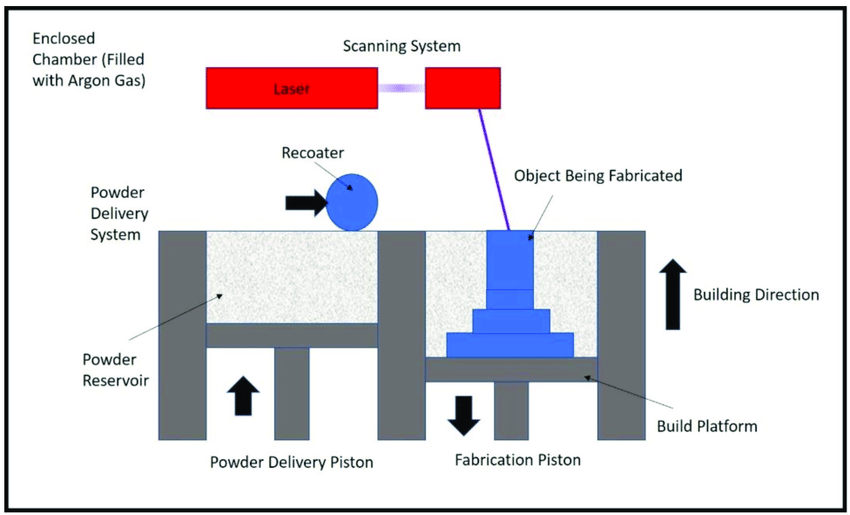
Selective Laser Melting (SLM)
Principle: Operates similarly to DMLS, but ensures complete powder melting, yielding a uniform material bond.
Advantages: The finished products are robust and have a superior surface finish.
Disadvantages: It’s a costly procedure that often requires additional post-processing.
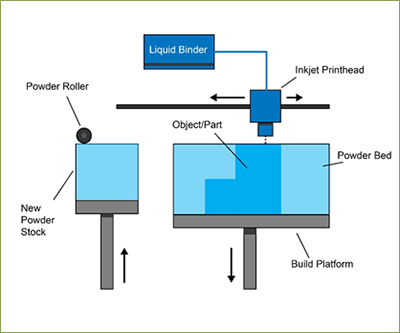
Binder Jetting
Principle: A binder is dispersed onto the metal powder, effectively “binding” it. The product is subsequently solidified in an oven.
Advantages: Efficient process that supports the printing of expansive items with reduced material usage.
Disadvantages: Inferior strength when juxtaposed with other techniques and necessitates further solidification.
Technology | Core Principle | Strengths | Limitations |
DMLS | Melting layers of metal powder via laser | Precise, intricate designs, low waste | High cost, requires post-print refinement |
EBM | Melting metal powder in a vacuum via electron beam | Efficient with dense metals, less post-print stress | Time-consuming, high equipment cost |
SLM | Complete powder melting for consistent bonding | Robust output, superior finish | Expensive, needs added refining |
Binder Jetting | Binding metal powder, followed by furnace solidification | Quick, suitable for large prints, material-economical | Lower strength, requires post-print solidification |
Selecting the Right Technology for Metal 3D Printing
The optimal choice in metal 3D printing technology relies heavily on specific project requirements, allocated budget, and the desired attributes of the end product.
Available Materials for Metal 3D Printing
The progression in metal 3D printing has ushered in an expanded array of materials. Each metal comes with distinct properties, making it apt for various applications.
Material | Features | Applications | Characteristics |
Steel | Durable, corrosion-resistant, diverse alloys with varying traits | Automotive, aerospace industries, construction | High strength, corrosion resistance |
Titanium | Lightweight, strong, biocompatible | Aerospace industry, medical implants | High strength, lightweight, corrosion resistance |
Aluminum | Lightweight, good thermal conductivity, corrosion-resistant | Automotive industry, electronics, aerospace | Lightweight, good electrical and thermal conductivity |
Bronze | Robust, corrosion-resistant | Artistry, jewelry, machine components | High strength, corrosion resistance |
Precious Metals | Valuable, appealing appearance, chemical resistance | Jewelry, dental applications, electronics | Corrosion resistance, high electrical conductivity |
Keeping in line with the project’s objectives and requirements, engineers have the discretion to select the most apt material. For instance, titanium, owing to its biocompatibility, becomes a prime choice for medical implants. Simultaneously, the allure and innate properties of precious metals earmark them for jewelry crafting.
Advantages of Metal 3D Printing
Metal 3D printing arms designers and manufacturers with avant-garde avenues and benefits, which are challenging to replicate with conventional metal processing methods. A quick exploration reveals:
- Intricate and Bespoke Designs: The flexibility to design and craft products with unparalleled and intricate design nuances.
- Material Efficacy: Contrasting traditional metalwork which sees considerable wastage, 3D printing is judicious in material application, thereby curbing waste.
- Speedy Turnaround: A direct transition from a digital blueprint to a tangible entity is feasible, eliminating dependency on dedicated molds or tools.
- Cost-effective Prototyping: Rapid and economically efficient prototype creation accelerates research, thereby trimming down both time and cost associated with product development.
Metal 3D printing, with its array of benefits, undeniably stands as an invaluable asset in the toolkit of contemporary engineers and manufacturers.
Potential Hurdles in Metal 3D Printing
- Intrinsic Restrictions:
- Boundary Limitations: Despite its flexibility, there exist constraints regarding minimal thickness, part precision, and crafting fine elements. Additionally, the cooling phase might induce product deformations.
- Financial Considerations:
- Capital Investments & Material Expenses: Initial procurement costs for 3D printing setups are significant. The price of certain metal powders, particularly for mass production, can tilt the economic balance.
- Post-Printing Endeavors:
- Additional Refinements: Post-production often mandates further enhancements, be it for desired surface finishes, thermal treatments for mechanical property enhancement, or eliminating the printing support structures.
Hence, when mulling over 3D metal printing adoption, a holistic understanding, encapsulating both its advantages and inherent challenges, is paramount.
Metal 3D Printing Across Verticals
- Aerospace:
- Lightweight Yet Robust: Catering to the stringent requirements of the aviation sector, 3D metal printing molds complex, lightweight components, influencing an aircraft’s fuel efficacy.
- Medical Sphere:
- Tailored Implants: Metal 3D printing’s precision proves pivotal in sculpting patient-specific implants, thus enhancing surgical results and expediting recovery.
- Jewelry Craftsmanship:
- Intricate Elegance: Jewellers are harnessing 3D printing to birth complex, previously unattainable designs, also facilitating swift prototype creations.
- Automotive Realm:
- Fast-Track Prototyping: Automobile giants employ 3D printing for both prototype parts and final components, ushering in cost-savings and speed in crafting specialized parts.
- Innovation & Research:
- Research Aided by 3D: Metal 3D printing is becoming an essential tool in R&D labs. Its swiftness and cost-effectiveness are invaluable assets in experimental endeavors.
These instances elucidate the transformative potential of metal 3D printing, redefining methodologies in varied sectors.
Metal 3D Printing: A Glimpse into the Future
Research and Innovation in Technology and Materials
Focus is currently being directed towards the development of novel metal powders and alloys. These advancements aim to offer enhanced mechanical properties, be more amenable to machining, or exhibit specific attributes like electrical conductivity and resistance to elevated temperatures. Additionally, exploration into new printing technologies is underway, with objectives to amplify production speed, elevate product surface quality, and diminish process expenditures.
Development Forecasts and Potential Markets
Considering the current rate of advancement and the escalating intrigue in additive technologies, it’s anticipated that metal 3D printing will progressively command a larger portion of the manufacturing sector. This influence isn’t limited to the previously mentioned industries; it extends to sectors like construction, where distinctive metal components can be incorporated, and electronics, which often demand miniaturised metal parts.
It’s also projected that the geographical spectrum of 3D metal printing applications will broaden. With technological advancements and a dip in equipment expenses, nations previously dormant in this domain might soon emerge as frontrunners in the adoption and progression of additive methodologies.
In summation, the horizon of metal 3D printing captivates researchers, engineers, and business professionals alike. Emergent innovations hold the promise to metamorphose manufacturing paradigms and inaugurate markets brimming with unprecedented growth potential.
Concluding Thoughts on Metal 3D Printing
Metal 3D printing has emerged as a cornerstone of innovation in the contemporary manufacturing landscape. Echoing the ethos of Industry 4.0, this technology is reshaping the methods of conceptualizing, crafting, and refining products.
Impact of 3D Metal Printing on Today’s Manufacturing
Year after year, the footprint of metal 3D printing broadens, finding applications from aerospace to the medical field. This advancement paves the way for crafting intricate designs, diminishing product weight, consolidating components, and streamlining production timelines. Consequently, manufacturers are equipped to adapt swiftly to market dynamics, venture into novel designs, and deliver premium products to consumers.
Looking Ahead: Predictions and Potential
Evaluating the trajectory of additive manufacturing technologies, one can foresee metal 3D printing further integrating into conventional production realms and simultaneously discovering novel areas of utility. The fervent pursuit of research and the integration of groundbreaking materials and methods make the future of metal 3D printing all the more optimistic. Beyond refining current production techniques, it harbours the potential to usher in new industrial sectors and marketplaces.
To sum it up, metal 3D printing has set a transformative momentum in the manufacturing sector, and we’re merely witnessing its onset. A plethora of opportunities beckons, promising a brighter, more efficient future.
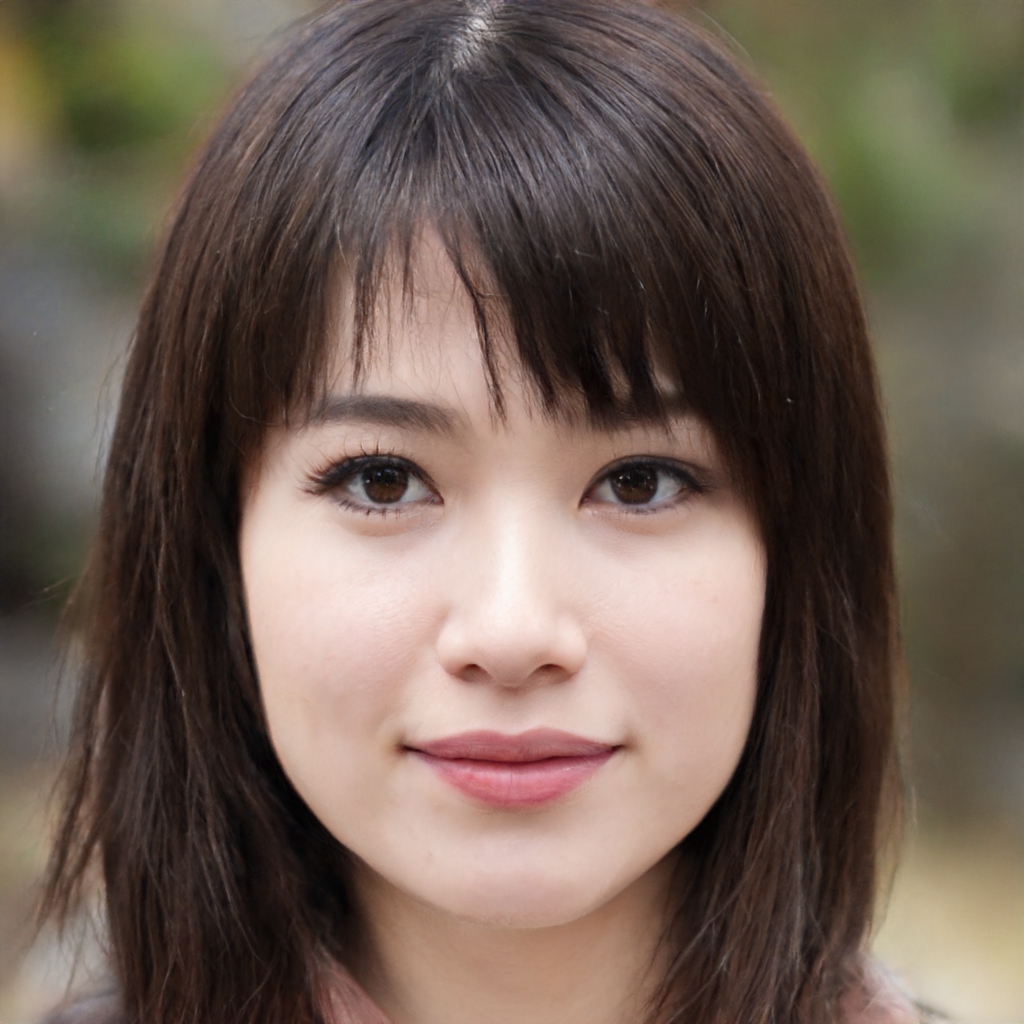
Eun-Ji is a journalist by training and a 3D enthusiast by nature. She studied journalism in university and has been writing ever since, but it was only recently that she discovered her love for 3D modeling.