Table of Contents
Introduction
3D printing, or additive manufacturing, is a cutting-edge process that fabricates three-dimensional objects layer by layer. Diverging from conventional manufacturing methods like casting or block cutting, this technology begins with a digital 3D model.
The Significance of 3D Printing in Today’s Industry and Society
The advent of 3D printing has revolutionized approaches to design, manufacturing, and innovation. In contemporary industry, it actively contributes to the creation of prototypes, customized parts, and functional end products. This technology affords businesses and engineers unique opportunities to reduce the time from idea to production, thereby saving valuable resources.
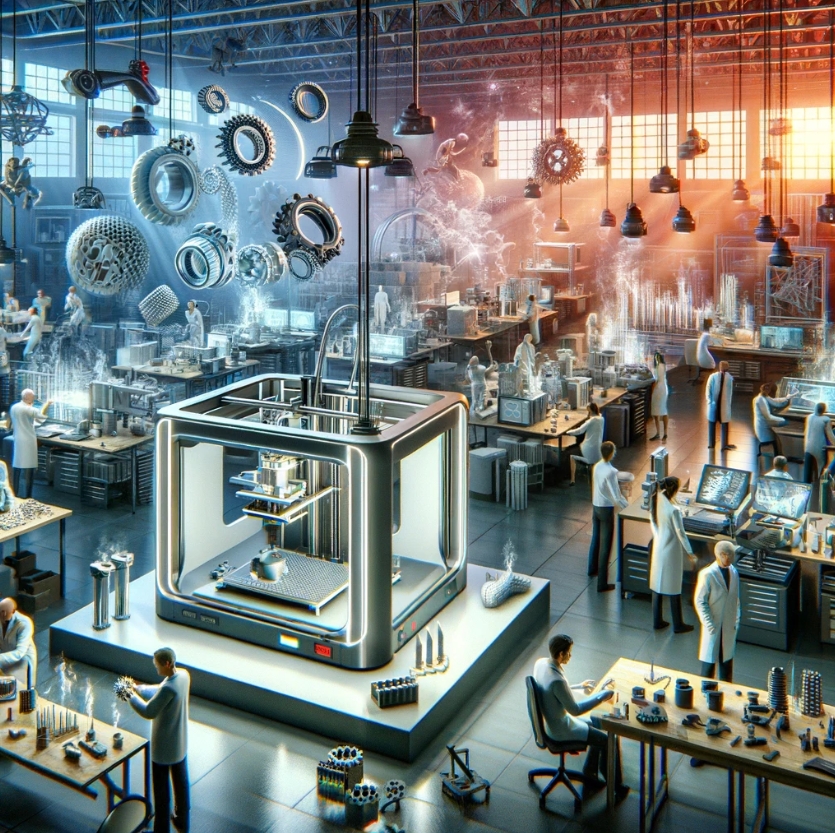
In society, 3D printing unlocks the doors to customization and personalization of products. Individuals can craft unique objects, artifacts, and even medical implants tailored to their specific needs. This transformative capability is reshaping the understanding of mass production, making it more adaptable and flexible.
Basic 3D Printing Technologies
Fused Deposition Modeling (FDM)
Working Principle
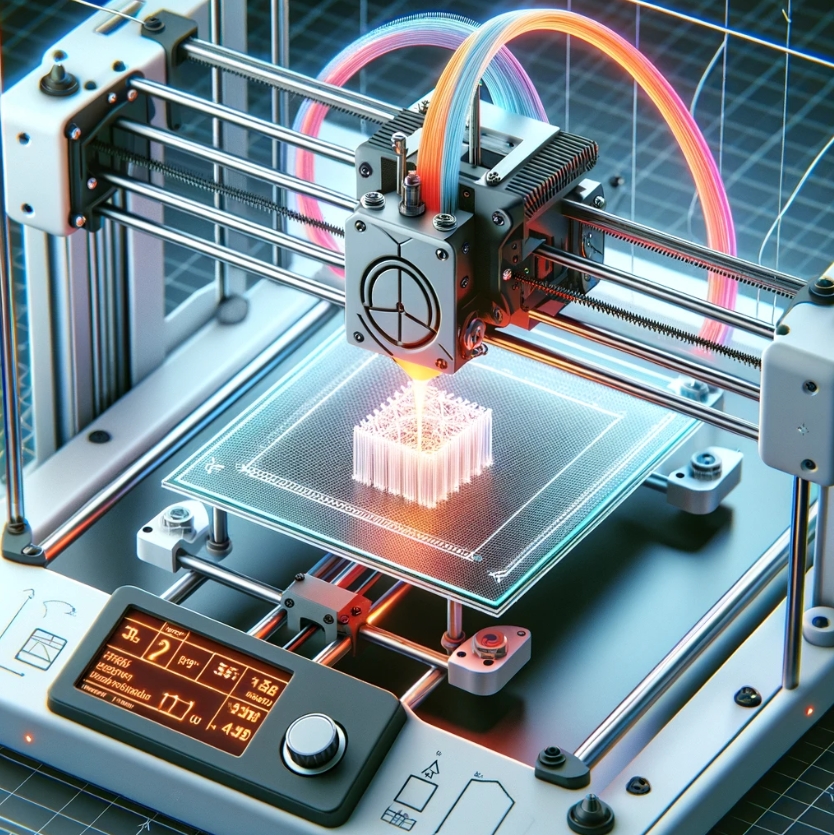
Fused Deposition Modeling (FDM), one of the most prevalent 3D printing technologies, operates by feeding a plastic filament through a heated extruder. The extruder then spreads the material, creating an object layer by layer as it moves along three-dimensional coordinates.
Advantages and Disadvantages
Advantages of FDM:
- Affordability and Low Cost: FDM printers are often more economical, appealing to home users and small businesses.
- Wide Choice of Materials: Supporting various plastic filaments such as PLA, ABS, PETG, FDM provides a versatile selection.
- Ease of Use: The FDM process is relatively straightforward, making it ideal for beginners.
Disadvantages of FDM:
- Low Resolution: FDM printing may have limited resolution compared to some other technologies, potentially impacting part quality.
- Visible Layers: Layering may result in visible lines, necessitating additional processing.
- Support Necessity: Printing objects with transitions in the air might require additional support structures that need subsequent removal.
Despite its set of advantages and disadvantages, FDM technology remains widely used due to its affordability and user-friendly nature.
Stereolithography (SLA)
Working Principle
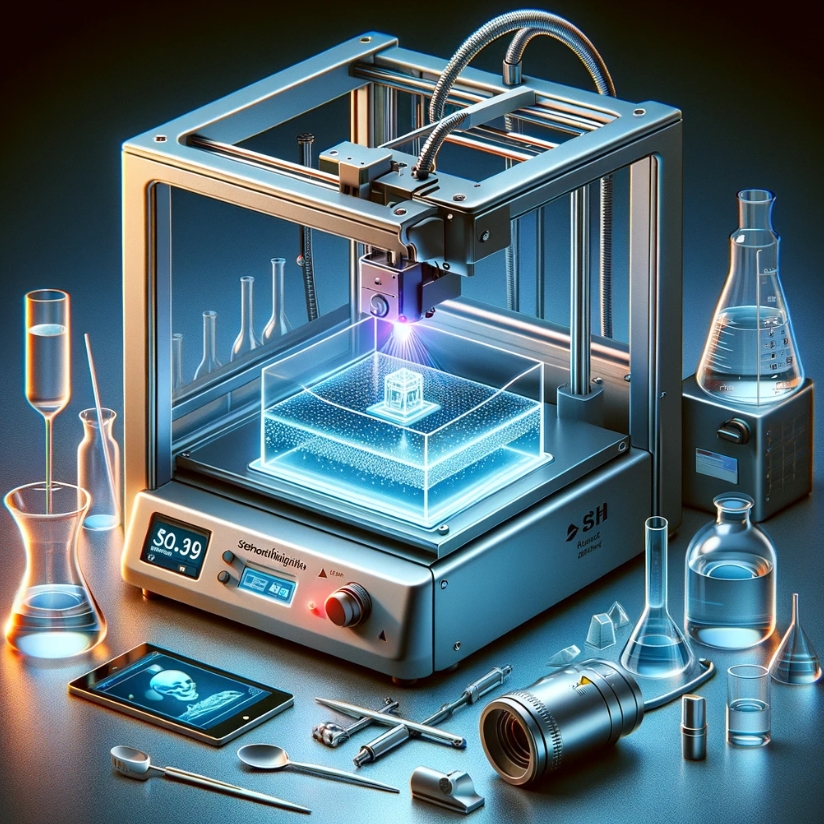
Stereolithography (SLA) relies on ultraviolet light to polymerize liquid resin. An SLA printer comprises a liquid resin reservoir and an ultraviolet laser. The laser focuses on the resin’s surface, causing polymerization and hardening. The print is then dropped onto the layer, and the process repeats until the object is complete.
Advantages and Disadvantages
Advantages of SLA:
- High Resolution: SLA provides high-quality printing with excellent resolution, ideal for intricate parts.
- Smooth Surface: The use of liquid resin allows the creation of objects with a smooth surface, minimizing visible layers.
- Support for Complex Shapes: SLA excels in printing complex geometries and precision parts.
Disadvantages of SLA:
- Limited Material Choice: Material options in SLA may be more restricted compared to FDM, though advancements in resin formulas are addressing this limitation.
- High Equipment Cost: SLA printers are often more expensive, posing a potential obstacle for small businesses and hobbyists.
- Post-Processing Requirement: Some SLA-printed models may require post-processing to remove supports and polish surfaces.
Stereolithography technology stands as a powerful tool for those prioritizing high quality and precision in 3D printing, despite some limitations in materials and equipment costs.
Selective Laser Sintering (SLS)
Principle of Operation
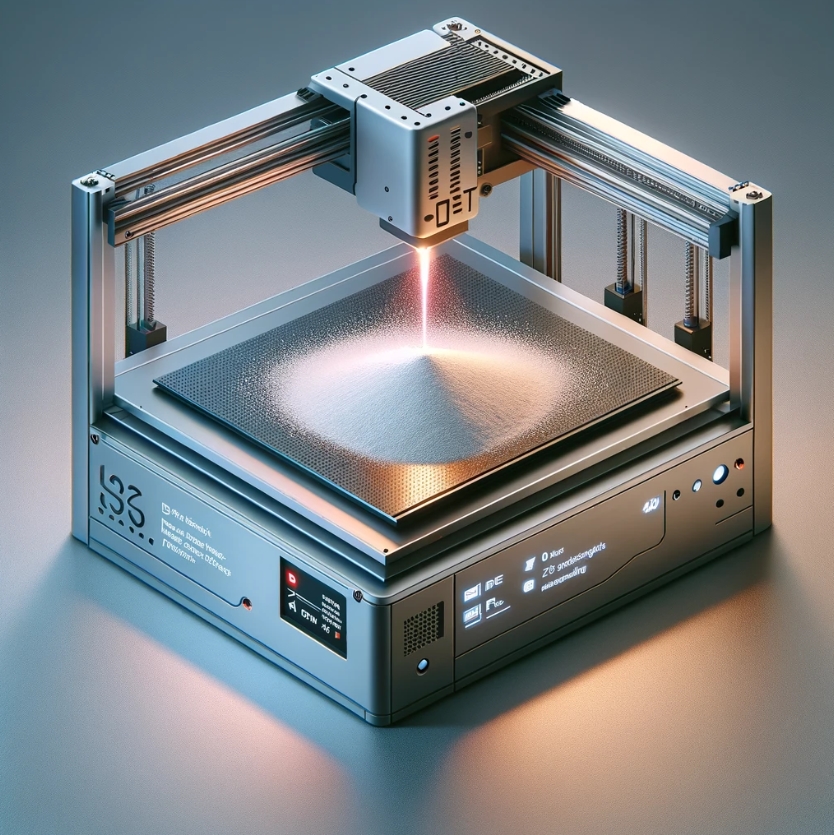
Selective Laser Sintering (SLS) utilizes a laser to synthesize thin layers of powder material. The SLS printer features a platform where the powder layer is spread, and a laser spot-heats and synthesizes selected areas, bringing powder particles together. When a layer is complete, the platform lowers, and the process repeats for the next layer.
Advantages and Disadvantages
Advantages of SLS:
- Wide Material Choice: SLS accommodates various materials, including plastics, metals, and ceramics, making it versatile for diverse applications.
- No Need for Supports: As the powder acts as its own support, additional support structures are unnecessary, simplifying the printing of complex geometries.
- Production of Functional Prototypes: SLS enables the creation of prototypes that not only mimic the final product’s appearance but also possess functionality.
Disadvantages of SLS:
- High Equipment Cost: Similar to SLA, SLS technology equipment is typically expensive, potentially limiting access for small businesses.
- Limited Print Sizes: Some SLS printers may impose restrictions on the size of printable objects, posing a disadvantage for large-scale projects.
- Work Environment Requirements: The powder sinterization process demands controlled temperature and humidity, necessitating specific working conditions.
SLS offers a broad material selection and the ability to produce functional prototypes but comes with considerations of equipment cost, size limitations, and work environment requirements.
Other Technologies
Digital Light Processing (DLP)
Principle of Operation
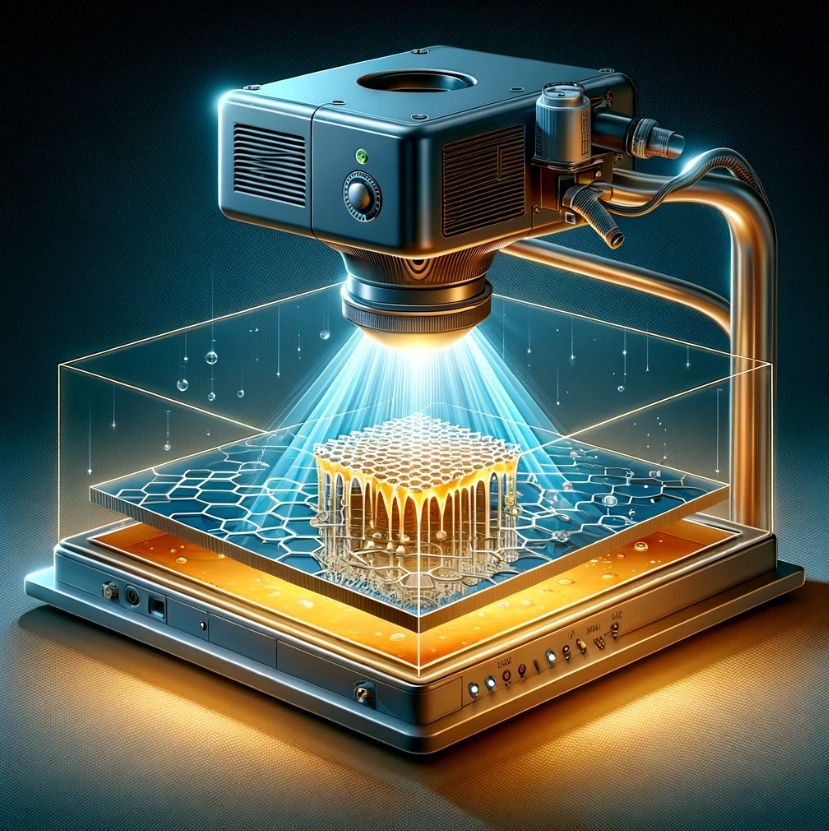
Digital Light Processing (DLP) shares similarities with SLA, but instead of a laser, a light projector projects an image of each layer onto the surface of liquid resin. The resin cures upon exposure to light, forming layers and creating a three-dimensional object.
Advantages and Disadvantages
Advantages of DLP:
- High Print Speed: DLP generally achieves a faster print speed than SLA, thanks to simultaneous radiation affecting multiple dots.
- Accuracy and Resolution: DLP technology offers high accuracy and resolution, making it appealing for creating detailed elements.
Disadvantages of DLP:
- Limited Materials: Similar to SLA, material choices may be limited, though ongoing advancements in resin formulas are addressing this limitation.
- Post-Print Finishing Requirement: Some DLP-printed models may require polishing and the removal of supports after the printing process is complete.
Electron Beam Melting (EBM)
Principle of Operation
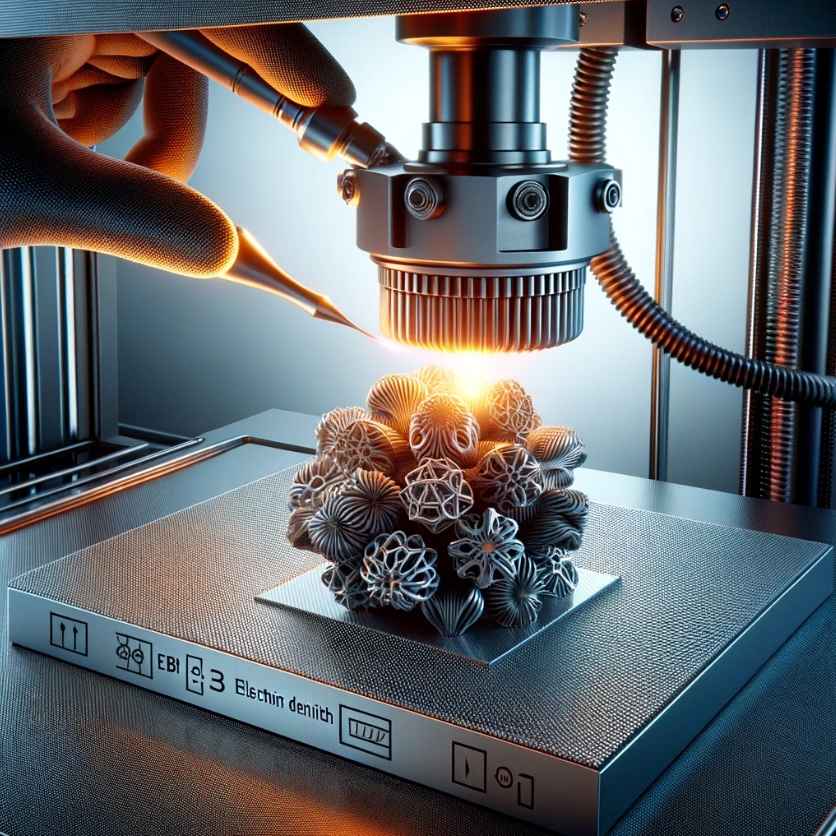
Electron Beam Melting (EBM) involves using an electron beam to melt metal powder, resulting in the creation of three-dimensional metal objects. This process imparts high density and strength to the printed products.
Advantages and Disadvantages
Advantages of EBM:
- High Strength: EBM produces parts with a high degree of strength, making it well-suited for manufacturing robust metal components.
- No Need for Supports: Typically, supports are not required, simplifying the process and enabling the printing of complex shapes.
Disadvantages of EBM:
- High Equipment Cost: EBM equipment is expensive, limiting accessibility for many businesses.
- Material Limitations: The choice of metal materials may be limited compared to other technologies.
Laminated Object Manufacturing (LOM)
Principle of Operation
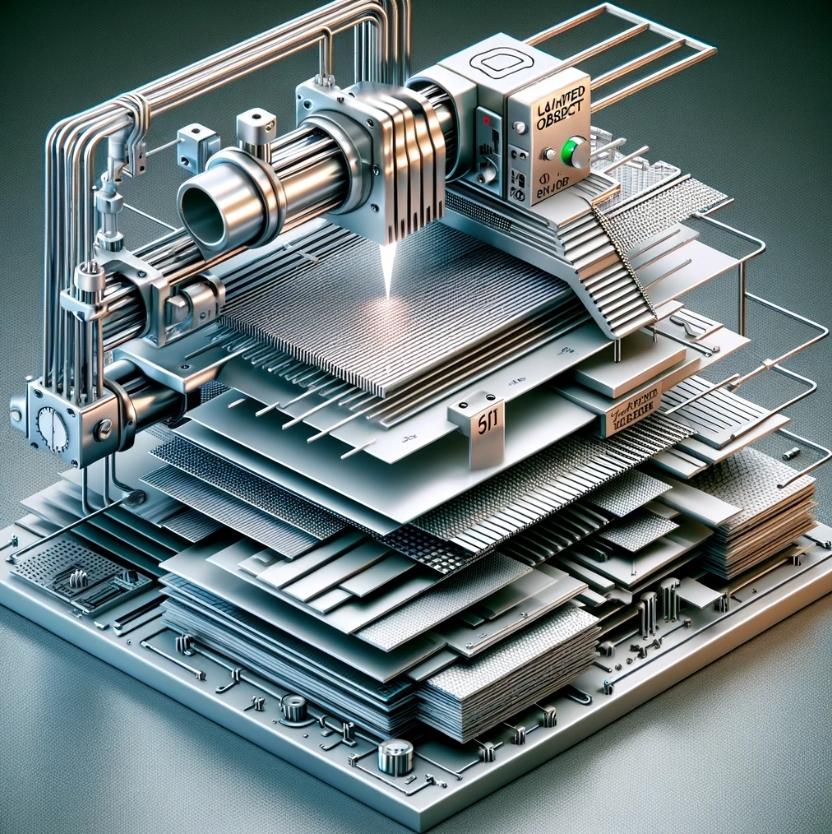
Laminated Object Manufacturing (LOM) involves bonding layers of paper, plastic, or metal using a laser or adhesive. Excess material is then removed, and the process repeats to create a three-dimensional object.
Advantages and Disadvantages
Advantages of LOM:
- Low Material Cost: LOM’s use of paper and readily available materials makes it more cost-effective.
- Large Print Sizes: LOM can accommodate large sizes of printed objects, suitable for expansive projects.
Disadvantages of LOM:
- Limited Resolution: LOM may have limited resolution compared to some other technologies.
- Difficulty in Creating Complex Geometries: The overlaying and gluing layers process may pose challenges in creating intricate designs.
Each of these technologies presents unique characteristics, and the choice depends on specific project needs, budget considerations, and material requirements.
Materials for 3D Printing
Plastic Materials
PLA (Polylactide)
Description
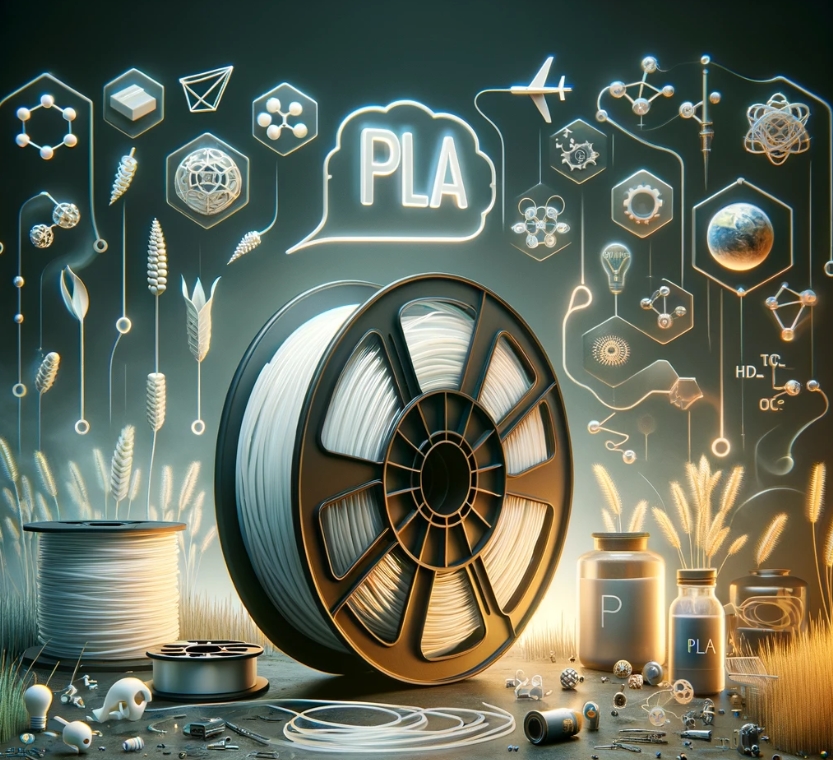
PLA, or polylactide, is a biodegradable and environmentally friendly plastic derived from natural resources like corn starch or cane. Its popularity is attributed to environmental friendliness and ease of use.
Advantages and Disadvantages
Advantages of PLA:
- Eco-friendly: PLA is biodegradable and renewable, surpassing the environmental friendliness of some other plastics.
- Low Toxicity: PLA printing generally emits minimal harmful fumes, ensuring safe home use.
- Wide Color Spectrum: Available in various colors, PLA enables vibrant and diverse patterns.
Disadvantages of PLA:
- Lower Temperature Resistance: PLA exhibits lower temperature resistance than certain plastics, limiting its suitability for high-temperature applications.
- Less Durable: Relative to some materials, PLA may lack strength, impacting durability.
ABS (Acrylonitrile Butadiene Styrene)
Description
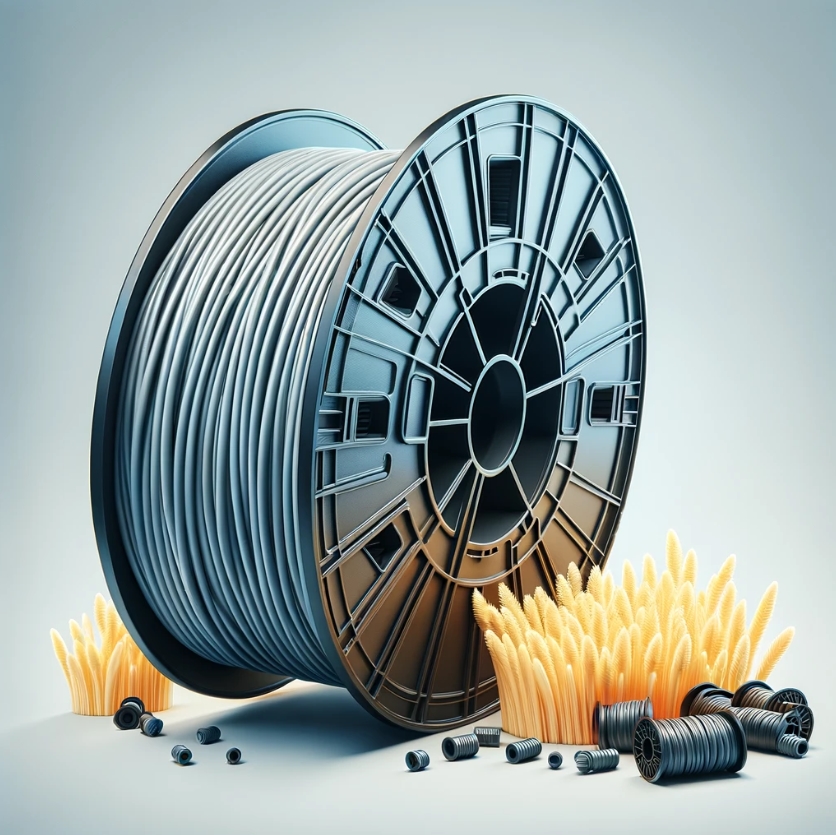
ABS is a thermoplastic polymer composed of three monomers: acrylonitrile, butadiene, and styrene. Widely used in 3D printing, ABS is known for its strength and high-temperature resistance.
Advantages and Disadvantages
Advantages of ABS:
- High Strength: ABS is renowned for its strength, making it suitable for durable and functional parts.
- High Temperature Resistance: It retains mechanical properties at high temperatures, ideal for applications requiring heat resistance.
- Post-printability: ABS responds well to post-printing treatments such as sanding and coloring.
Disadvantages of ABS:
- Emits Vapors: ABS can emit vapors during printing, requiring well-ventilated areas for use.
- Prone to Warping: Rapid cooling, especially over large areas, can cause warping in ABS prints.
PETG (Polyethylene Terephthalate with Glycol)
Description
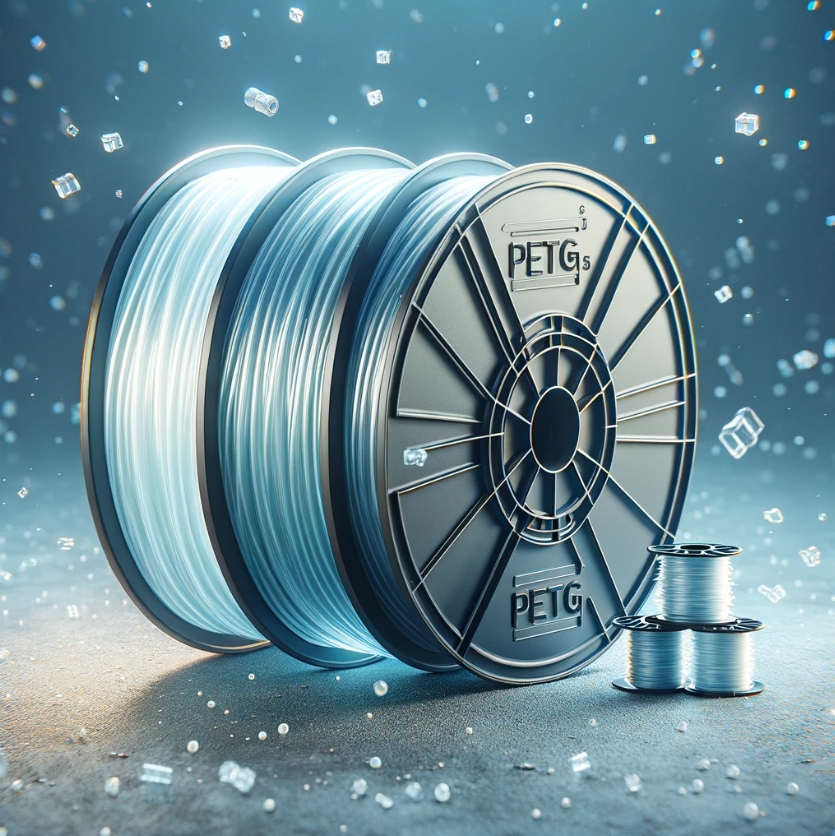
PETG is a durable and transparent plastic combining the strengths of PLA and ABS. It excels in creating transparent and impact-resistant parts.
Advantages and Disadvantages
Advantages of PETG:
- Transparency: PETG boasts high transparency, making it an excellent choice for transparent parts.
- Strength and Resilience: Combining ABS strength with PLA resilience, PETG is resistant to impact.
- Good Chemical Resistance: PETG is resistant to many chemicals, expanding its application range.
Disadvantages of PETG:
- More Difficult to Print: PETG may require precise printer settings and can be more challenging to print than PLA.
- Less UV Resistance: PETG can be sensitive to UV rays compared to some other materials.
Metal Materials
Powder Metals
Description
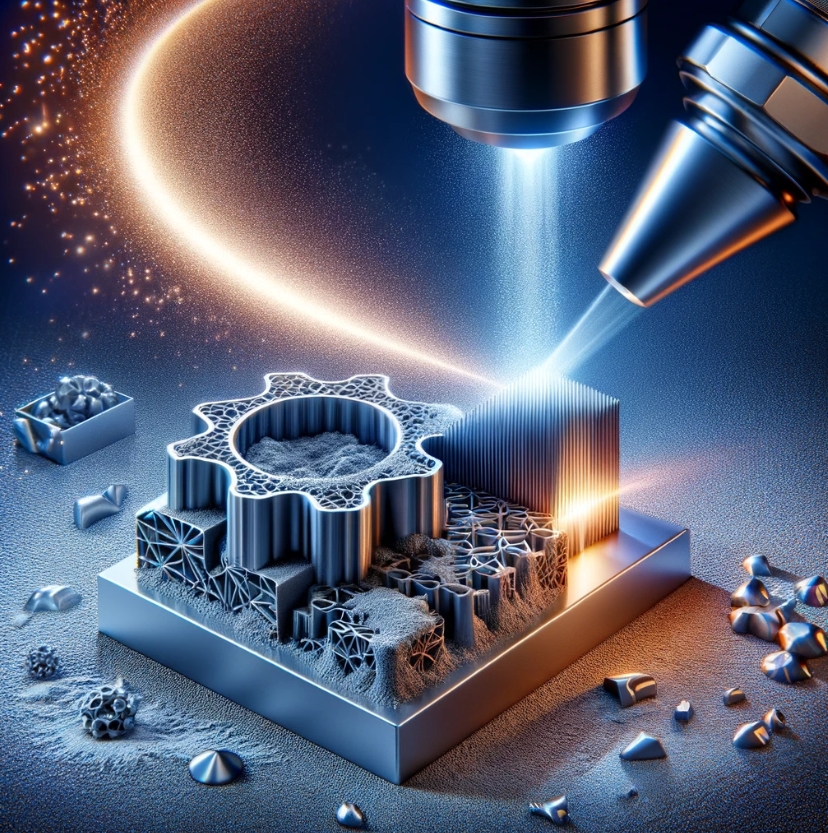
Powder metals find extensive use in metal 3D printing. This process involves applying a thin layer of metal powder, followed by using a laser or electron beam to melt or sinter the powder, forming a solid metal layer.
Advantages and Disadvantages
Advantages of Powdered Metals:
- High Strength: 3D printing with metal powders yields high strength and mechanical resistance.
- High Thermal Conductivity: Metal parts exhibit excellent thermal conductivity, suitable for high-temperature applications.
- Wide Selection of Metals: The technology allows the use of various metals, including aluminum, titanium, stainless steel, and more.
Disadvantages of Powdered Metals:
- Difficulty in Processing: Printing with metal powders demands fine-tuned equipment and specific processing conditions.
- High Cost: Equipment and materials for metal 3D printing can be expensive, limiting accessibility for some businesses.
Alloys for Metal 3D Printing
Description
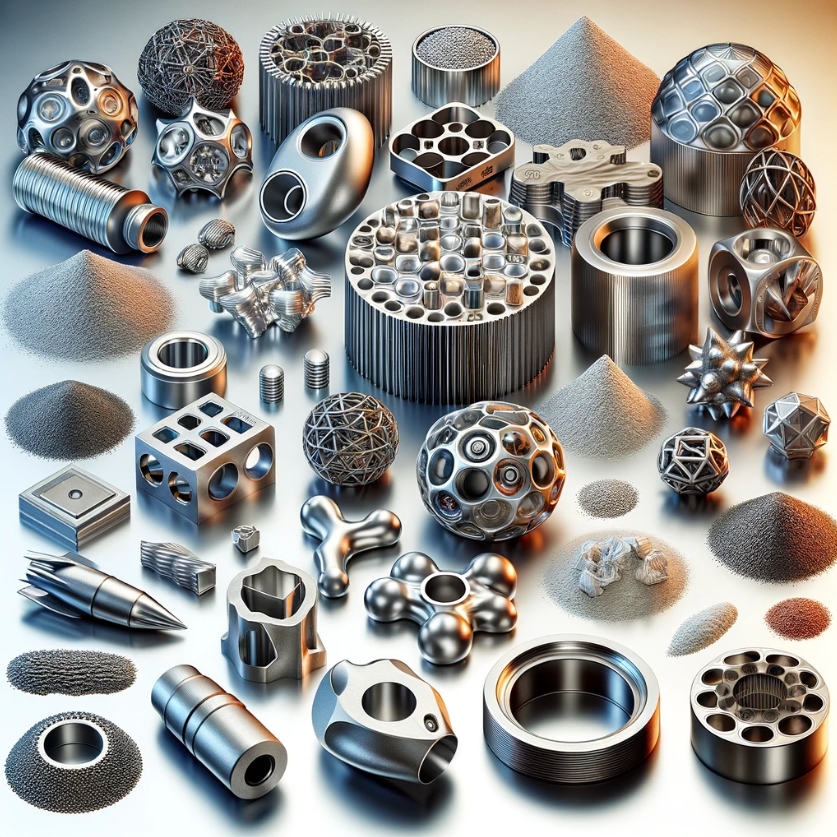
Alloys for metal 3D printing include various metals and elements, offering unique properties like high strength, thermal conductivity, and corrosion resistance.
Advantages and Disadvantages
Advantages of Alloys for Metal 3D Printing:
- Specialized Properties: Alloys can be customized for specific applications, providing desired properties like heat resistance or magnetic characteristics.
- Aerospace Applications: Metal 3D printing alloys are widely used in the aerospace industry for creating lightweight and strong components.
Disadvantages of Metal 3D Printing Alloys:
- Difficulty in Processing: Similar to metal powders, printing alloys requires highly customized equipment.
- Cost: Creating parts from metal alloys can be an expensive process, limiting accessibility for all businesses.
Metal 3D printing offers unique opportunities to create durable and complex metal parts, despite technological and financial challenges.
Biomaterials
Medical Applications
Description
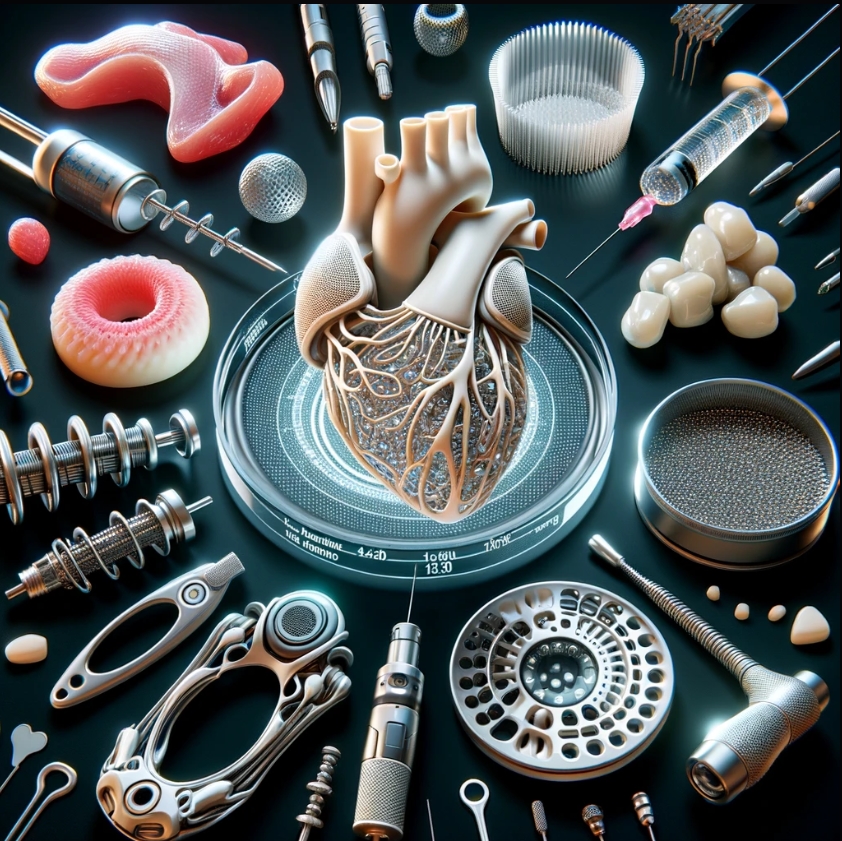
Biomaterials in the context of 3D printing offer opportunities to create objects combining advanced mechanical properties with biocompatibility. In the medical field, biomaterials are widely used for custom implants, prosthetics, and other medical devices.
Advantages and Disadvantages
Advantages of Medical Applications of Biomaterials:
- Customization of Treatment: 3D printing of biomaterials enables personalized medical solutions, considering the unique anatomical features of the patient.
- Biocompatibility: Biomaterials provide high biocompatibility, reducing the risk of rejection and increasing implant success.
- Creation of Complex Structures: 3D printing allows the creation of intricate structures, including thin capillaries and mesh formations, useful for recreating biological tissues.
Disadvantages of Medical Applications of Biomaterials:
- Difficulty of Validation: The validation process of biomaterials for medical purposes requires rigorous testing, making it challenging to adopt new technologies.
- Limited Choice of Materials: Currently, there is a limited selection of biomaterials available for 3D printing, and developing new ones requires time and resources.
Development Perspectives
Integration with Biological Systems
Development prospects include integrating biomaterials with biological systems, enabling the creation of functional organs and tissues. Advances in bioprinting may lead to the possibility of creating viable organs for transplantation.
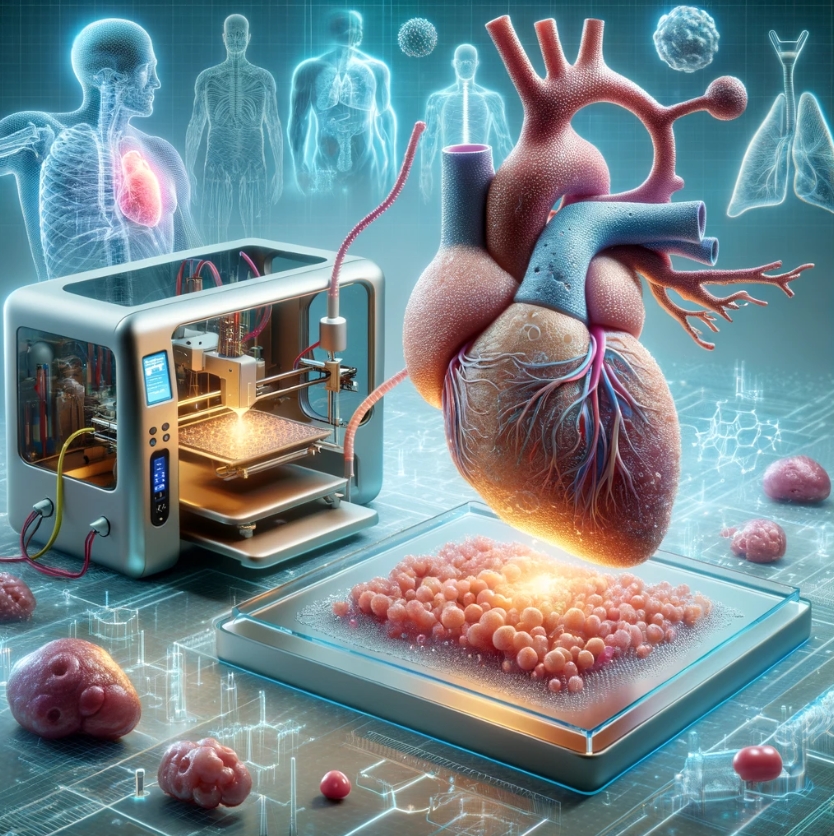
Development of New Materials
One of the key areas of focus is the development of new biomaterials that provide not only high biocompatibility but also specific properties such as elasticity or thermal stability.
Bioprinting Technology
The development of bioprinting technology, allowing precise placement of cells and biomaterials, will be a key factor in creating complex biological structures.
3D printed biomaterials offer tremendous promise for the medical industry, and their further development could lead to revolutionary changes in the field of transplantation and the creation of customized medical solutions.
Application of 3D Printing in Various Industries
Manufacturing
Description
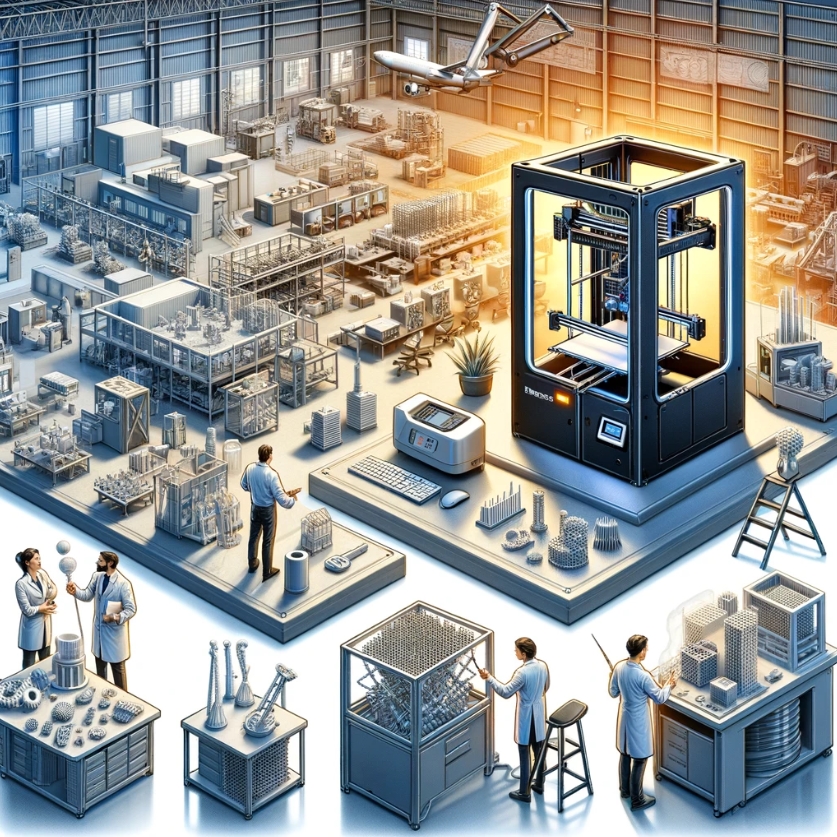
3D printing has become integral to the manufacturing industry, particularly in the prototyping process. This stage of product development has become more efficient and cost-effective due to the ability to quickly create physical models of products.
Advantages
Advantages of Prototyping Using 3D Printing:
- Reduced Development Time: 3D printing allows prototypes to be created in a matter of hours, significantly reducing product development time.
- Cost Savings: The ability to use different materials and create complex parts within a single print reduces prototyping costs.
- Easy Access to Design Customization: Quickly changing designs and creating multiple prototyping options helps improve the product.
Low Production Volume
Description
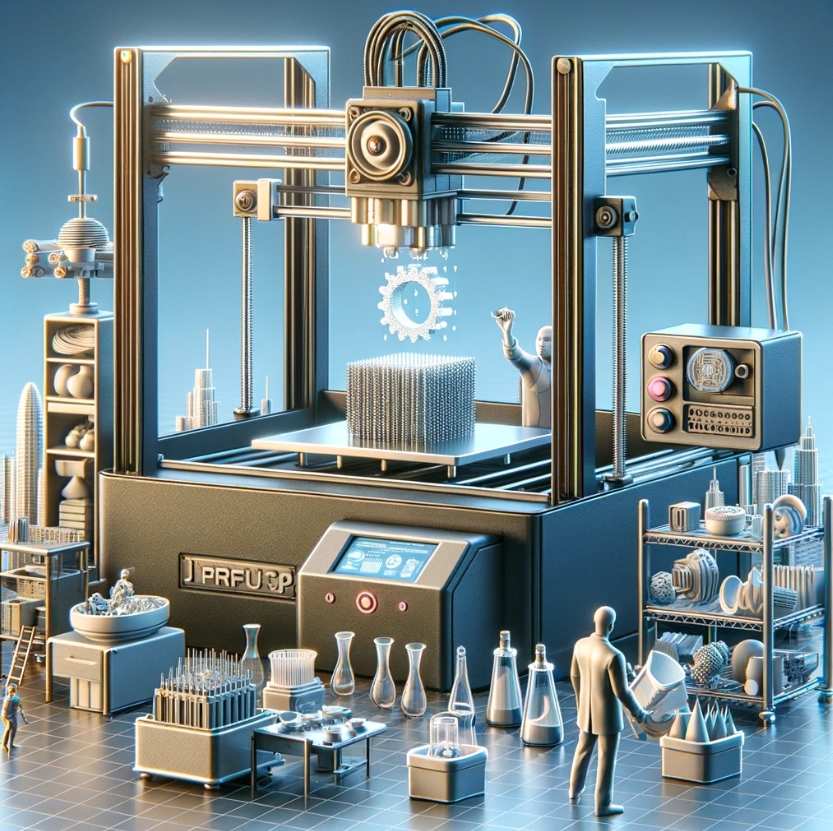
3D printing offers unique opportunities for low-volume manufacturing, especially in technologically demanding industries. This technology allows small batches of products to be manufactured at minimal cost.
Advantages
Benefits of Low-Volume Manufacturing Using 3D Printing:
- Time and Resource Savings: The ability to create complex parts without the need for complex molds and dies significantly reduces lead times and costs.
- Product Customization: 3D printing allows for the production of unique, personalized products, which is relevant in a consumer-driven industry.
- Material Efficiency: Minimal material waste in 3D printing reduces manufacturing costs.
3D printing has revolutionized prototyping and low-volume production processes, giving manufacturers flexible and cost-effective ways to create and test new products.
Medicine
Creation of Biomodels
Description

3D printing has found wide application in the medical field, especially in the creation of biomodels. These 3D models of human body parts are created from medical data, such as CT or MRI scans, and are used for surgical training, surgical planning, and educational purposes.
Advantages
Advantages of Creating Biomodels Using 3D Printing:
- Accurate Replica of Patient Anatomy: Biomodels accurately recreate the anatomical structure of a particular patient, allowing surgeons to better understand the complexities of surgeries.
- Surgical Training: Medical students and surgeons can use biomodels for training and practice before real surgeries.
- Planning Complex Surgeries: Surgeons can use biomodels to pre-plan and visualize complex surgical procedures.
Personalized Implants
Description
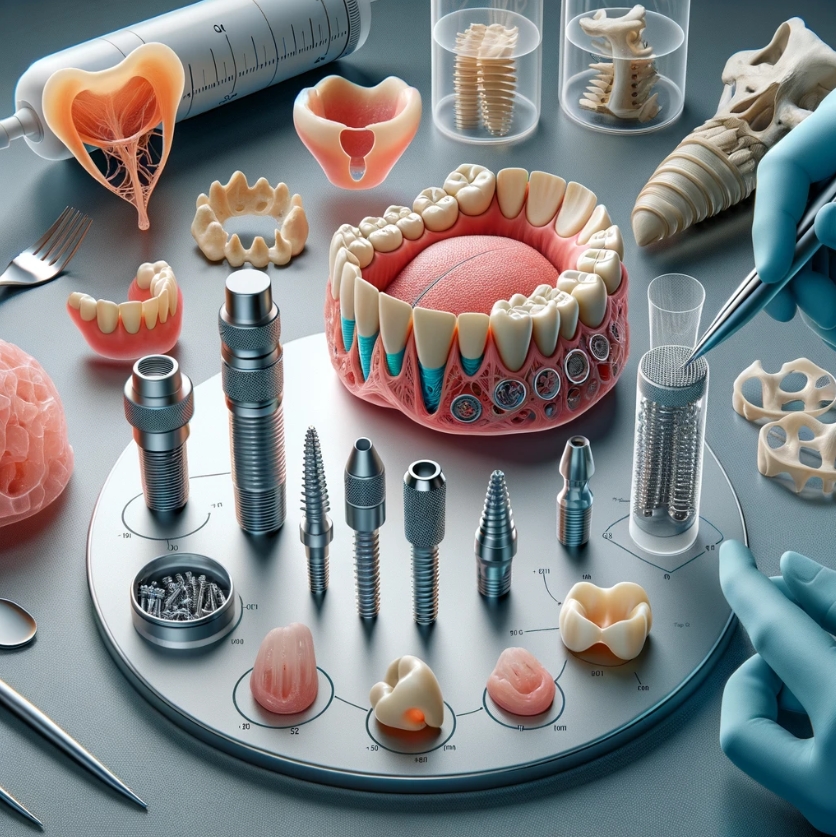
3D printing enables the creation of personalized implants tailored to a patient’s specific needs. This includes creating bone implants, dentures, and other medical devices that precisely match the patient’s anatomy.
Benefits
Benefits of Personalized Implants Using 3D Printing:
- Perfect Match to Anatomy: Personalized implants are created based on the individual patient’s data, ensuring a perfect match to the patient’s anatomy.
- Reduced Time and Risk: By precisely adapting to the anatomy, surgical time and the risk of possible complications are reduced.
- Improved Outcomes: Personalized implants improve the functionality and aesthetics of the reconstructed body parts.
3D printing in medicine plays a key role in personalizing treatment, improving surgical precision, and reducing patient recovery time.
Aerospace Industry
Lightweight and Strong Structures
Description
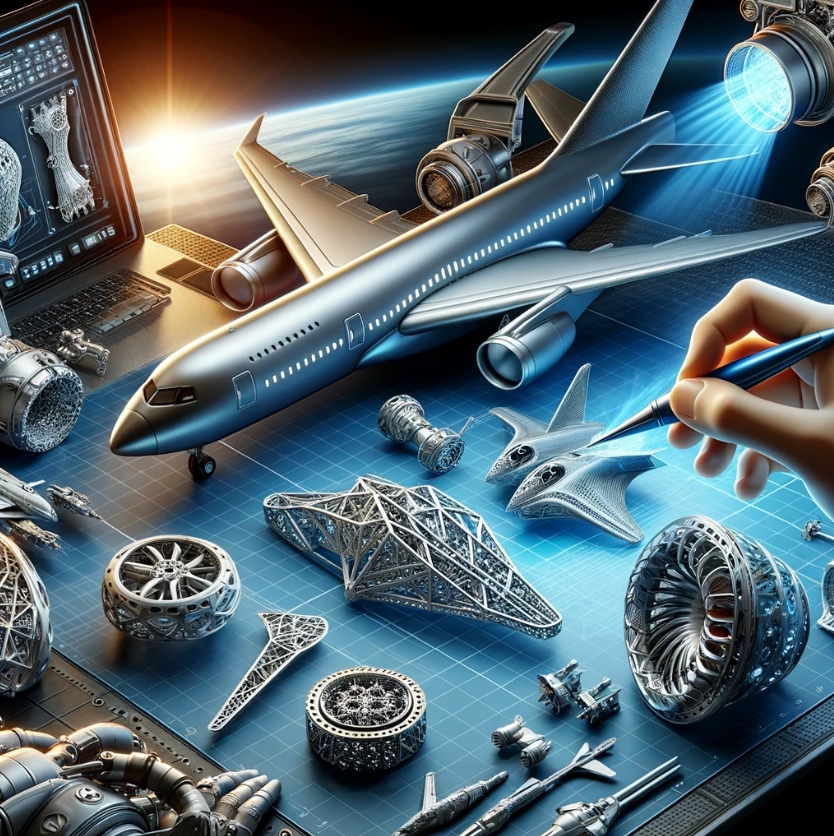
In the aerospace industry, 3D printing is being used to create lightweight and strong structures, which is becoming critical to reduce weight and improve the performance of aircraft and spacecraft.
Benefits
Advantages of Creating Lightweight and Strong Structures Using 3D Printing:
- Shape Optimization: 3D printing allows for the creation of complex geometric shapes, allowing structures to be optimized for maximum strength at minimum weight.
- Integration of Functional Elements: The ability to integrate functional elements directly into the design increases efficiency and reduces the number of separate parts.
- Reduced Material Intensity: 3D printing uses material only where it is needed, reducing material consumption and cost.
Reducing Weight and Increasing Efficiency
Description
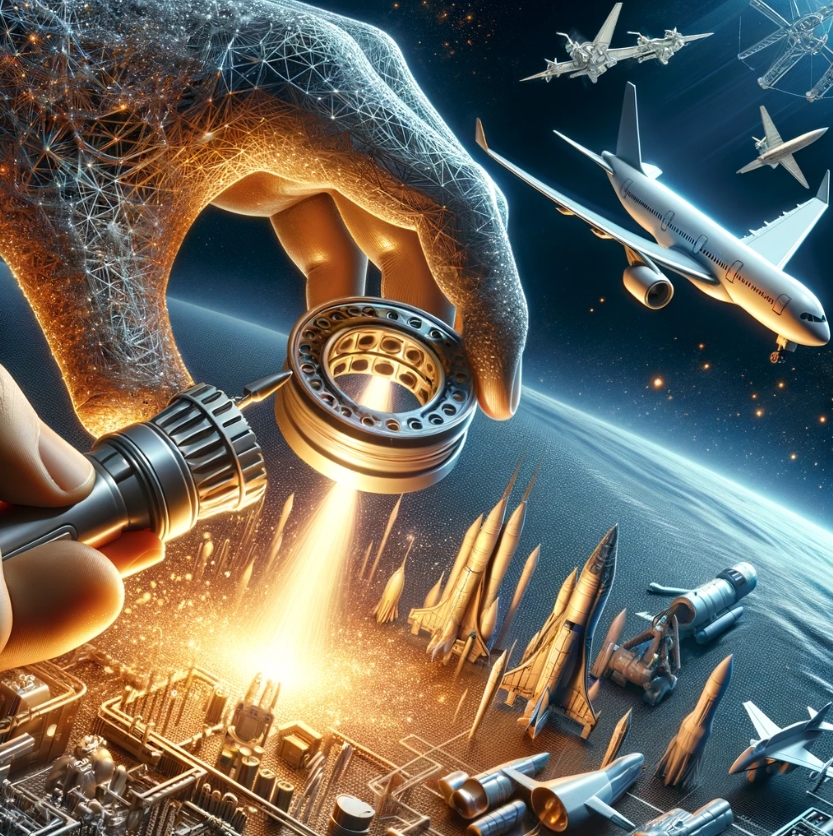
3D printing in the aerospace industry results in components that have optimal strength while minimizing weight, significantly reducing the mass of air and spacecraft.
Benefits
Advantages of Weight Reduction and Increased Efficiency Using 3D Printing:
- Fuel Savings: Reducing the weight of air and spacecraft results in lower fuel costs and increased range.
- Increased Maneuverability: Lightweight designs created using 3D printing provide increased maneuverability and overall vehicle efficiency.
- Cost Reduction: Improved efficiency and reduced material costs make component manufacturing more cost-effective.
3D printing plays a key role in the design and production of lightweight and durable structures in the aerospace industry, helping to improve efficiency and reduce operating costs.
Comparative Analysis
Equipment and Material Costs
Fused Deposition Modeling (FDM)
Equipment Cost: Generally, FDM 3D printers are more affordable compared to other technologies.
Material Cost: PLA filament used in FDM is cost-effective, while specialized filaments may be pricier.
Stereolithography (SLA)
Equipment Cost: SLA printers are often more expensive due to precision components like lasers or UV lights.
Material Cost: Resin materials used in SLA tend to be more costly than FDM filaments.
Selective Laser Sintering (SLS)
Equipment Cost: SLS printers are usually high-end and come with a higher price tag.
Material Cost: SLS uses powdered materials like nylon, which can be more expensive than FDM filaments.
Digital Light Processing (DLP)
Equipment Cost: DLP printers can have a varied cost range, with some models more affordable than SLA.
Material Cost: Resins for DLP can be comparable to SLA in terms of cost.
Technology | Equipment Cost | Material Cost |
Fused Deposition Modeling | Affordable | Cost-effective |
Stereolithography | Expensive | Moderate |
Selective Laser Sintering | High-end | Expensive |
Digital Light Processing | Varied | Comparable |
Print Speed and Resolution
Fused Deposition Modeling (FDM)
Print Speed: FDM printers generally have moderate print speeds, suitable for prototyping and low-volume production.
Resolution: FDM resolution is acceptable for many applications but may not achieve the fine detail of other technologies.
Stereolithography (SLA)
Print Speed: SLA printers can offer faster print speeds than FDM due to their layering technique.
Resolution: SLA provides high-resolution prints with fine details, making it suitable for intricate models.
Selective Laser Sintering (SLS)
Print Speed: SLS printers often have faster print speeds compared to FDM, especially for complex geometries.
Resolution: SLS can achieve high resolution, suitable for producing functional prototypes and end-use parts.
Digital Light Processing (DLP)
Print Speed: DLP can have rapid print speeds similar to SLA, making it efficient for certain applications.
Resolution: DLP offers good resolution, especially in the vertical direction.
Technology | Print Speed | Resolution |
Fused Deposition Modeling | Moderate | Acceptable |
Stereolithography | Fast | High |
Selective Laser Sintering | Fast (complex parts) | High |
Digital Light Processing | Rapid | Good |
Ease of Use and Maintenance
Fused Deposition Modeling (FDM)
Ease of Use: FDM printers are generally user-friendly, making them suitable for beginners.
Maintenance: Maintenance is usually straightforward, involving tasks like nozzle cleaning and bed leveling.
Stereolithography (SLA)
Ease of Use: SLA printers may have a steeper learning curve, requiring more precise calibration and handling of resin materials.
Maintenance: SLA printers often require careful resin handling and periodic cleaning of the resin tank.
Selective Laser Sintering (SLS)
Ease of Use: SLS printers are typically more complex and may require advanced knowledge, limiting their accessibility for beginners.
Maintenance: SLS printers may need more attention due to the use of powdered materials, requiring regular cleaning and maintenance.
Digital Light Processing (DLP)
Ease of Use: DLP printers share similarities with SLA but can be more user-friendly depending on the model.
Maintenance: Maintenance for DLP involves keeping the resin vat clean and ensuring the projector remains functional.
Technology | Ease of Use | Maintenance |
Fused Deposition Modeling | User-friendly | Straightforward |
Stereolithography | Learning curve | Resin handling, tank cleaning |
Selective Laser Sintering | Complex | Regular cleaning, powder handling |
Digital Light Processing | Varies | Resin vat, projector maintenance |
Trends in 3D Printing Technologies
New Materials and Their Properties
Advanced Polymers
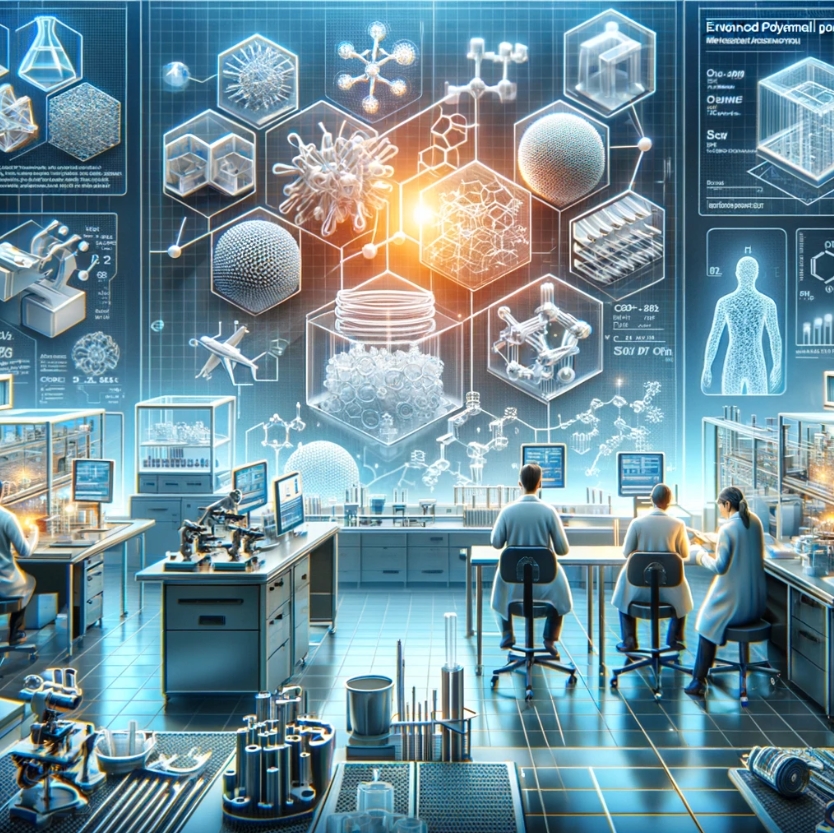
Ongoing research is dedicated to developing polymers with enhanced mechanical properties, heat resistance, and durability. This effort aims to expand the range of applications for 3D-printed parts.
Composite Materials
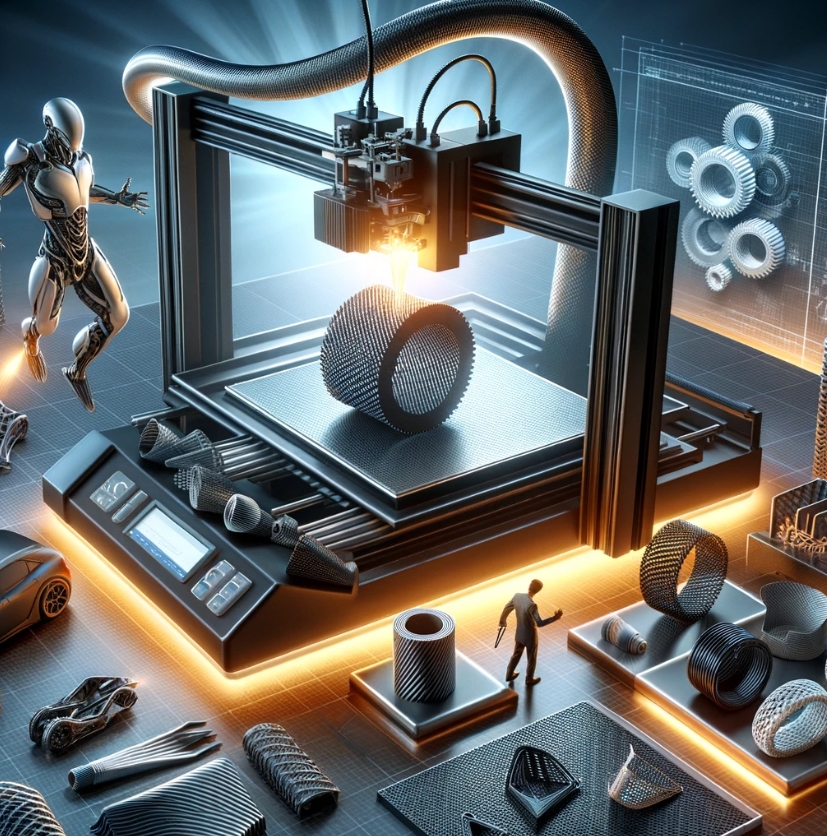
The integration of reinforced materials, such as carbon fiber or glass fiber, into 3D printing processes is geared towards creating parts with superior strength-to-weight ratios.
Bioinks
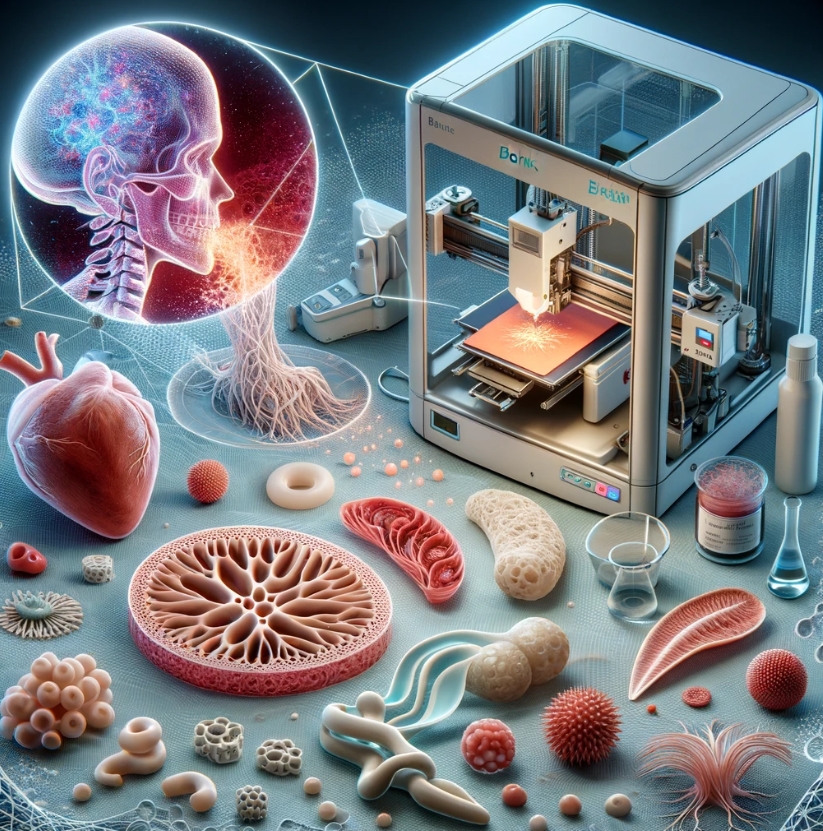
Advancements in bioprinting involve the development of bioinks that support the 3D printing of living tissues and organs. This groundbreaking technology paves the way for breakthroughs in regenerative medicine.
Improved Equipment Performance
Faster Print Speeds
Manufacturers are actively working on enhancing the speed of 3D printers across various technologies. This improvement enables quicker production of prototypes and end-use parts.
Larger Build Volumes
The trend towards larger build volumes accommodates the printing of more substantial components in a single run. This development increases the efficiency of 3D printing, particularly for larger-scale applications.
Multi-Material Printing
Advancements in multi-material 3D printing allow the simultaneous use of different materials within a single print. This provides greater versatility in material properties.
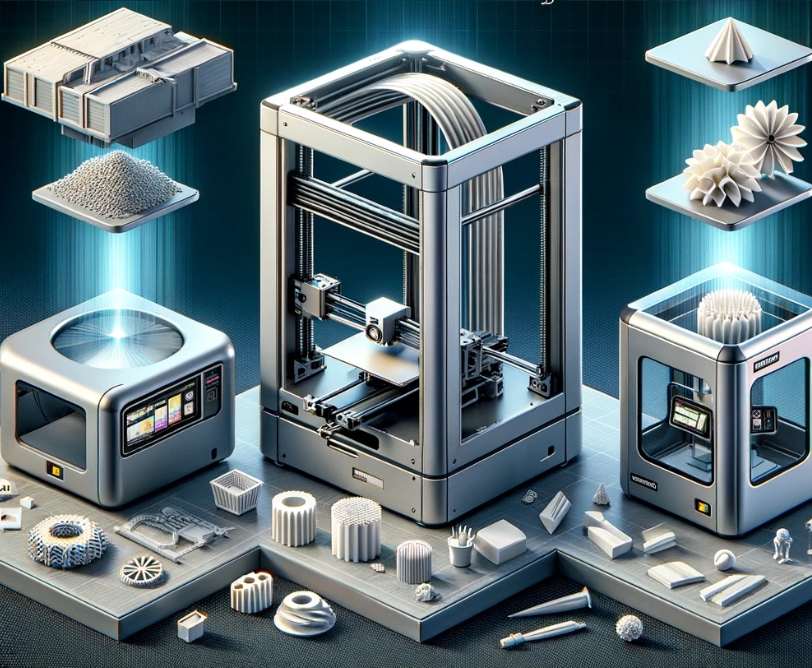
Advancements in 3D Printing Software
Design Software Integration
Software tools for 3D printing are evolving to seamlessly integrate with design software. This integration streamlines the transition from concept to print and enhances design capabilities.
AI and Generative Design
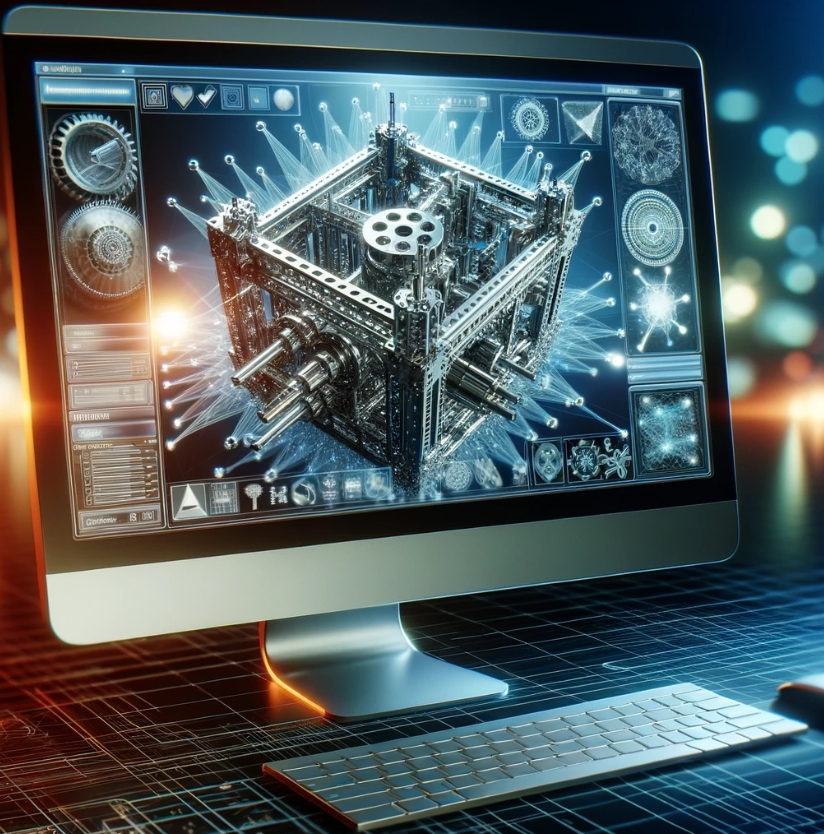
The integration of artificial intelligence (AI) and generative design algorithms allows for the creation of complex, optimized structures. This maximizes the efficiency and performance of 3D-printed parts.
Cloud-Based Printing Solutions
Cloud-based 3D printing solutions are gaining popularity, offering users remote access to printing capabilities, collaborative design features, and efficient file management.
The ongoing development of 3D printing technologies is characterized by a focus on material innovation, improvements in equipment performance, and advancements in software capabilities. These trends contribute to the continuous expansion of applications and the increasing adoption of 3D printing across various industries.
Conclusion
Summary of Comparative Analysis
In summarizing the comparative analysis of 3D printing technologies, each method displays unique strengths and weaknesses. Fused Deposition Modeling (FDM) stands out for its affordability and user-friendly nature, making it a preferred choice for prototyping. Stereolithography (SLA) excels in high resolution and speed, while Selective Laser Sintering (SLS) is recognized for producing robust, functional parts. Digital Light Processing (DLP) combines features from both SLA and FDM, offering a versatile solution.
Examining factors such as cost, speed, resolution, ease of use, and maintenance allows users to tailor their choice based on specific project requirements. The ongoing evolution of technology contributes to a dynamic landscape, providing diverse options for users with varying needs.
Forecast of 3D Printing Technology Development
The future of 3D printing holds exciting prospects. Anticipated advancements include the introduction of novel materials with superior properties, expanding the range of applications. Improved equipment performance, featuring faster print speeds and larger build volumes, is set to increase efficiency and scale in 3D printing projects. Software development, integrating artificial intelligence and cloud-based solutions, will further streamline the design-to-print process.
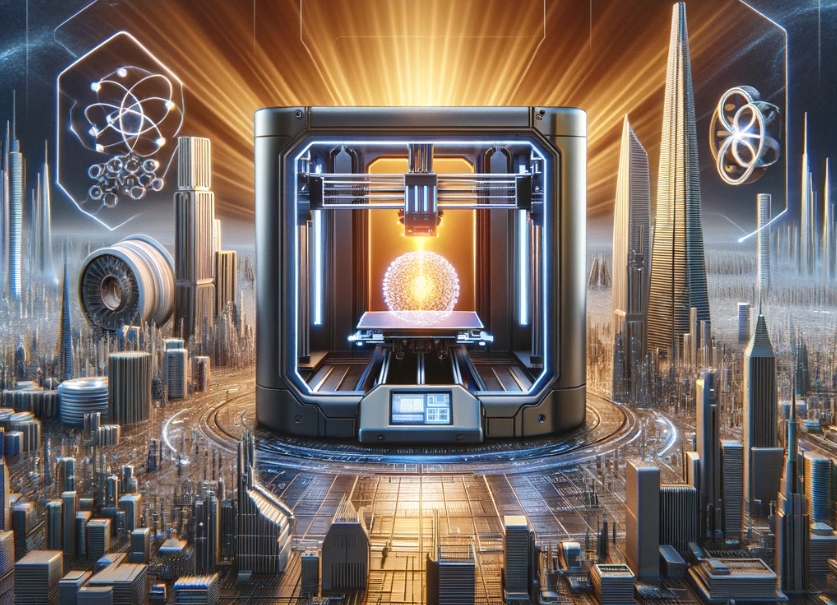
Significance of 3D Printing for Future Manufacturing and Innovation
The significance of 3D printing for the future of manufacturing and innovation cannot be overstated. This technology revolutionizes traditional production methods, offering unprecedented flexibility and customization. From healthcare to aerospace, 3D printing facilitates the creation of intricate designs, personalized medical solutions, and lightweight yet robust components. As it becomes more accessible, 3D printing is poised to drive innovation, transform supply chains, and usher in a new era of creativity in manufacturing.
In conclusion, the journey through the diverse landscape of 3D printing technologies reveals a field brimming with potential. As these technologies continue to advance, they will undoubtedly shape the future of how we design, create, and manufacture objects, ushering in a new era of possibilities and transforming the way we perceive and approach production.
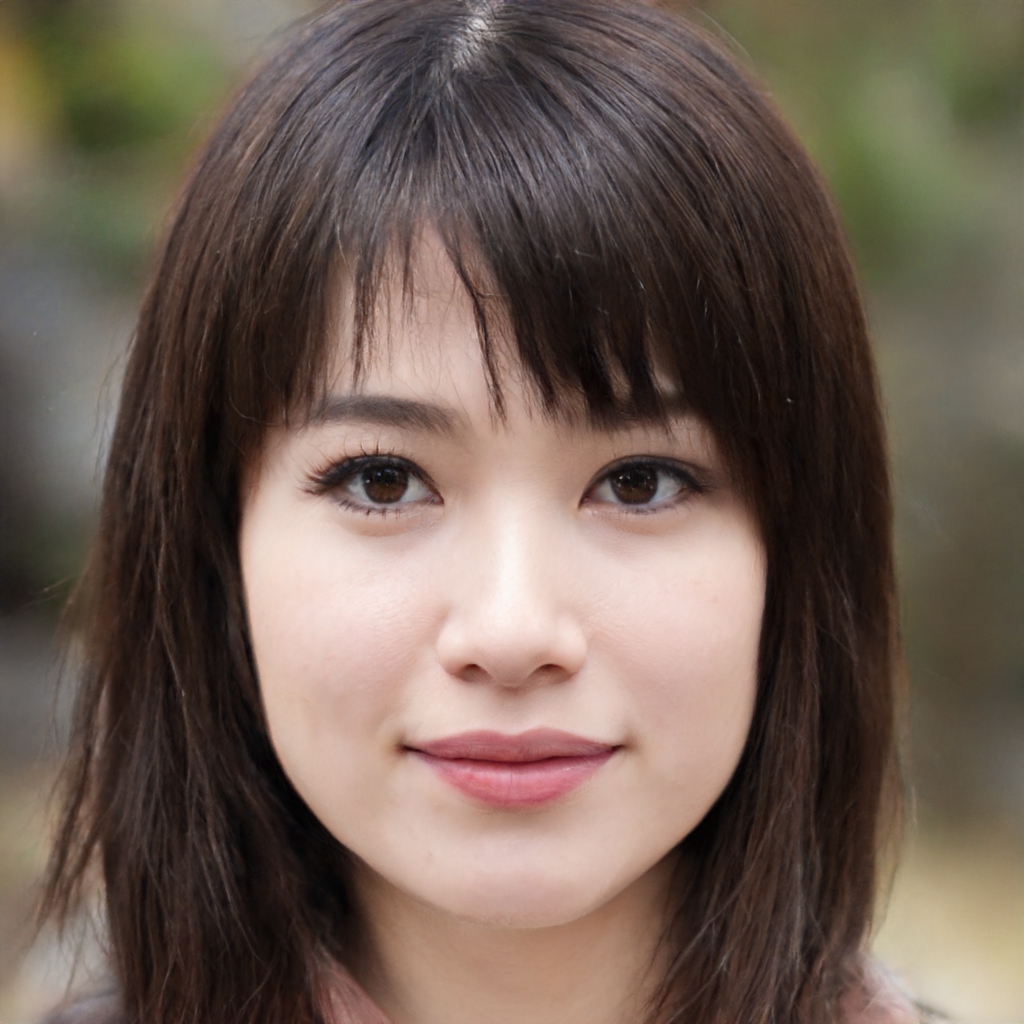
Eun-Ji is a journalist by training and a 3D enthusiast by nature. She studied journalism in university and has been writing ever since, but it was only recently that she discovered her love for 3D modeling.